von Nina Lümkemann, Annett Kieschnick, Bogna Stawarczyk
Sind die mechanischen Eigenschaften der neu entwickelten 3D-Druck-Materialien mit den Ergebnissen anderer Herstellungstechniken vergleichbar? Im Artikel wird basierend auf einer aktuellen Untersuchung darauf eingegangen.
Die additiven Technologien mit Fokus auf den 3D-Druck rücken immer mehr in den Praxis- und Laboralltag. Einige Technologien, wie zum Beispiel die Stereolithografie (SLA) und das Digital Light Processing (DLP), haben sich bereits in der Zahnmedizin etabliert und decken ein breites Indikationsspektrum ab (z. B. Modelle). Limitierender Faktor stellt derzeit die Entwicklung geeigneter polymerbasierter 3D-Druck-Materialien dar, die den Anforderungen als Medizinprodukt der Klasse IIa genügen und dauerhaft im Mund des Patienten eingesetzt werden dürfen.
3D-Druck im Vergleich zu anderen Fertigungsverfahren
Derzeit verfügbare Materialien sind insbesondere für die Herstellung von Aufbissschienen und Bohrschablonen, und damit für den kurzweiligen Einsatz, von großem Interesse. Beim Herstellen von Schienen mittels 3D-Druck (auftragend) kann im Vergleich zur frästechnischen Herstellung (abtragend) deutlich Material eingespart werden. Im Vergleich zur konventionellen Herstellung mittels Injektionstechnik stehen beim 3D-Druck das Einsparen von Zeit und Prozesssicherheit im Vordergrund.
Doch wie steht es um die mechanischen Eigenschaften der neu entwickelten 3D-Druck Materialien? Sind diese mit den Ergebnissen anderer Herstellungstechniken (frästechnisch aus PMMA-Rohling und konventionell mittels Injektionsverfahren) vergleichbar? Die vorliegende Untersuchung bewertet die Bruchlast und Abrasionsbeständigkeit eines 3D-Druck-Schienenmaterials im Vergleich zu frästechnischen und konventionellen Herstellung.
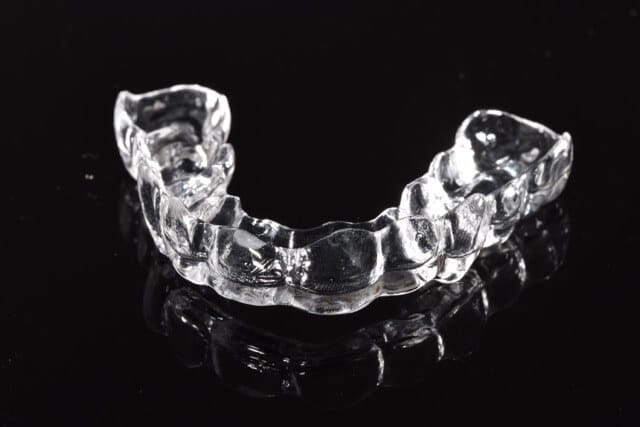
Untersuchungsaufbau
Für die Untersuchung wurden Prüfkörper in Form von Kronenkäppchen zur Simulation einer Aufbissschiene mittels drei unterschiedlicher Herstellungsverfahren hergestellt:
- 3D-gedruckt (DLP-Technologie) aus Schienenmaterial
- Frästechnisch aus PMMA-Rohling
- Konventionell mittels Injektionsverfahren
- Alle Prüfkörper wurden auf Hochglanz poliert und auf einem Metallstumpf befestigt.
Alle Prüfkörper wurden auf Hochglanz poliert und auf einem Metallstumpf befestigt.
Die Bruchlast wurde sowohl initial als auch nach einer künstlichen Alterung im Kausimulator (120.000 Zyklen, 37° C) untersucht. Zur Ermittlung der Abrasionsbeständigkeit wurden okklusale Abformungen angefertigt und mit dem Laserscanner digitalisiert, um den Materialverlust der Prüfköper nach 20.000 sowie 120.000 Kauzyklen zu untersuchen. Der Materialvolumenverlust wurde berechnet und die Gesamtheit aller Daten statistisch ausgewertet.
Ergebnisse
Die gefrästen Käppchen erzielten im Vergleich zu den 3D-gedruckten und den konventionell hergestellten Käppchen die höchste initiale Bruchlast. Nach der künstlichen Alterung im Kausimulator zeigten wiederum die gefrästen Käppchen die höchsten Werte, gefolgt von den 3D-gedruckten Käppchen. Die konventionell hergestellten Käppchen erzielten die geringste Bruchlast.
Für die gefrästen und konventionell hergestellten Käppchen führte die künstliche Alterung zu einer Abnahme der Stabilität, während die Werte der 3D-gedruckten Käppchen nicht beeinflusst wurden. Hingegen zeigten die 3D-gedruckten Käppchen den größten Materialvolumenverlust (Abrasion), gefolgt von den gefrästen Käppchen. Die konventionell hergestellten Käppchen zeigten die höchste Abrasionsbeständigkeit.
Schlussfolgerung
3D-gedruckte Kronenkäppchen zeigten eine geringere Abrasionsbeständigkeit und geringere Bruchlast als gefräste oder konventionell hergestellte Käppchen. Aus diesem Grund ist die Anwendung von 3D-gedruckten Aufbissschienen aus dem untersuchten Material nur für kurze Zeit zu empfehlen. Weitere Entwicklungen für die Schienenmaterialien, die im 3D-Druck mittels DLP-Technologie verarbeitet werden, sind notwendig.
Fazit für den Praxis- und Laboralltag:
Aufgrund der geringen Abrasionsbeständigkeit und der Bruchlast können 3D-gedruckte Aufbissschienen nur für einen Zeitraum von bis zu einem Monat im Mund des Patienten verbleiben. Dieser Wert entspricht auch dem Zeitraum, für den das Material derzeit zugelassen ist.
Publikation: Lutz A-M, Hampe R, Lümkemann N, Eichberger M, Stawarczyk B. Fracture resistance and 2-body-wear of 3-dimensional printed occlusal devices. J Prosthetic Dent 2018 [epub ahead]